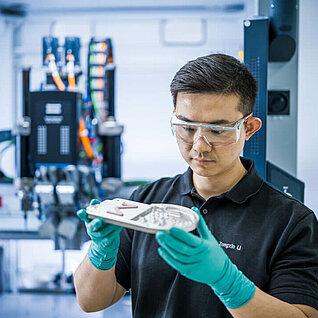
Dispensing with added value
The component is ready, the production processes are fully coordinated, production gets under way – but the results are disappointing. The problem is the dispensing process. So what’s the reason? Well, in order to develop a dispensing process that is perfectly suited to a particular project, it’s not enough simply to provide a dispensing system with the right parameters. Experience and know-how are indispensable here.